Plant Manager
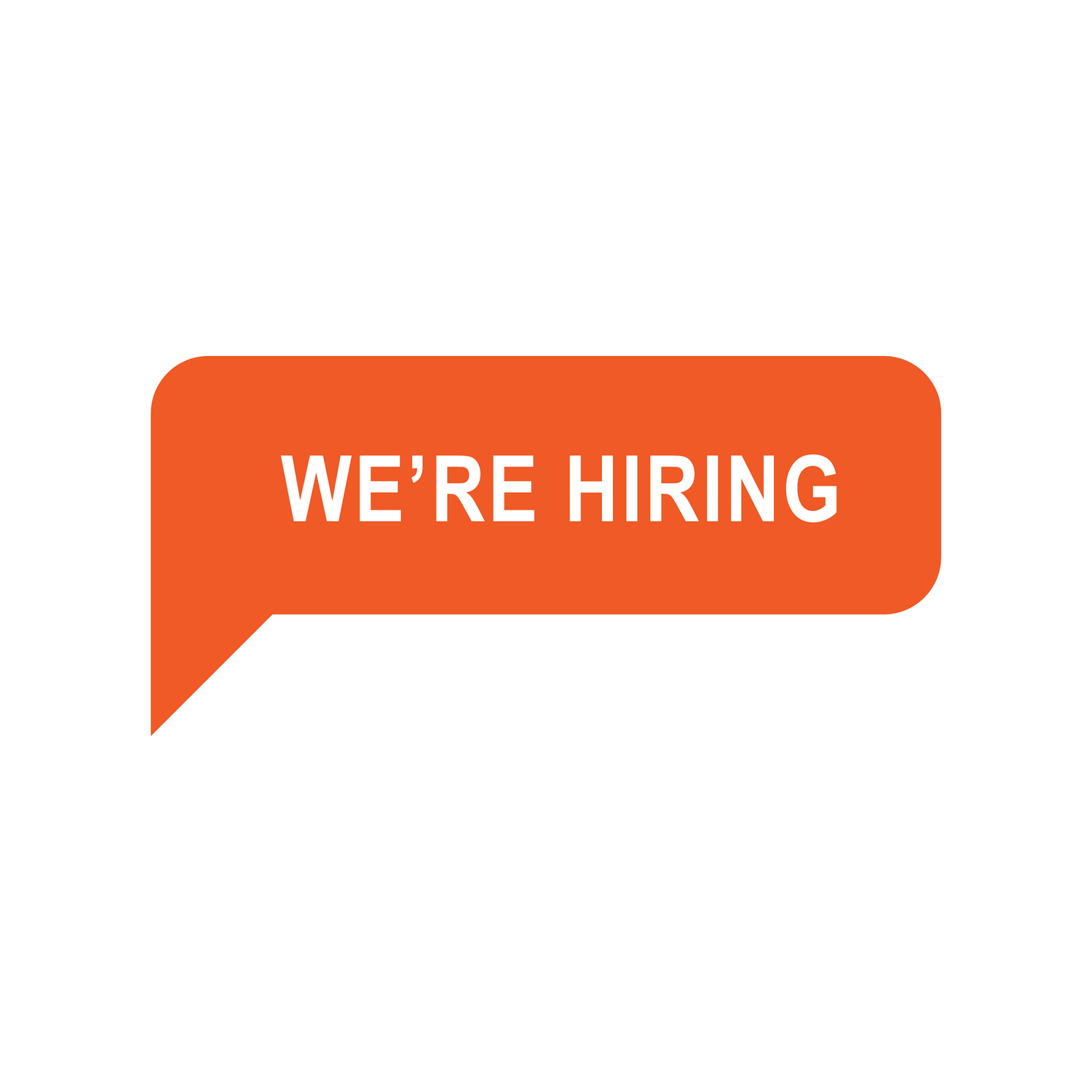
Premium Waters Inc
2024-10-04 05:44:59
Douglas,
Georgia,
United States
Job type: fulltime
Job industry: Manufacturing Operations
Job description
Do you want to work for a company that cares about it's people, healthy products and community in which we live and work? This is your opportunity to be a part of a growing organization that contributes to the safety of our communities through our people, The general purpose of our Plant Manager position is to serve his or her location and team with support functions to accomplish equipment installations, personnel hiring, orientation, and training; organizational design, and development of SOP's related to a successful plant operation. The Plant Manager will oversee, manage and continually improve the day-to-day operation of a multi-line bottling and blow molding facility. The Plant Manager will have overall responsibilities for production and production-related activities ensuring quality products are manufactured safely, and in a timely manner, while meeting cost objectives. The Plant Manager duties will also include leading by example, helping to develop teams, and preparing subordinates for future opportunities in a growth market.
EDUCATION and/or EXPERIENCE
Ten years related production leadership experience with a minimum of two years plant management experience; Associate or Bachelor degree in related field; or equivalent combination of education and experience. Knowledge of blow molding technology is a plus. LOCAL candidates are preferred.
ESSENTIAL DUTIES & RESPONSIBILITIES
Leadership
- Must have a proven ability to motivate and develop teams to continually improve performance. The individual should have experience in developing training for their exempt staff. They must also provide for the training needs of the plant, with plans put in place to address any training deficiencies. This person should display enthusiasm and the ability to get others to "buy in" to a team based approach that allows focus on company/plant goals.
- Establish mutual expectations to include all employees. Ensure clear goals are established as well as measurement and celebratory methodology.
- Lead by example: Demonstrate how people should be treated; how to address discipline, how to manage the over achievers and under performers.
- Work with others to solve problems using internal and external resources. Support decisions made with data, investigation, and problem-solving discussion.
- Facilitate meetings to build teams and communication between employees so that people understand the status of customer service, production, downtime, and scheduled repairs in the plant.
- Help all employees understand the importance of follow up by leading by example as well as ensuring others meet commitments.
- Champion initiatives in the department to institutionalize Safety, Quality, Lean Manufacturing, Team Development and Continuous Improvement.
Business/General
- Establish and monitor plant KPI's to ensure products conform to established customer and company standards; ensure timely communication occurs with all teams reviewing performance against goals.
- Provide leadership and support to Lean Business Practices and Activities.
- Review inventory levels and scheduling to maximize customer service while minimizing total overall cost.
- Assist in the hiring, training and staff evaluation to ensure customer needs are met while minimizing overtime and over crewing.
- Ensure plant cleanliness and application of GMP and HACCP policies; plant should be "Inspection Ready" at all times.
- Prepare and submit capital equipment recommendations, process changes, and building improvements.
- Ensure policies and procedures are followed in the plant.
- Demonstrate safety in all activities; Lead by example and expect others to follow safety practices.
FOOD SAFETY AND QUALITY OVERSIGHT RESPONSIBILITIES:
- Customer specs./BOM
- Water type/TDS/ PH/ Conductivity
- Bottles/color/ size
- Caps/labels
- Coding/bottle-case
- Packaging - wrap/corrugated/glue
- Pallets - pattern/height/wrap/chep-brown
- Documentation
- Plant oversight of Product Quality, GMP's, Pre-requisites, HACCP and SQF
FOOD SAFETY/QUALITY TRAINING:
- HACCP
- SQF
- GMP's
- Pest Control
- Documentation
- CPO
SKILLS:
- Demonstrated ability to lead people and get results.
- Ability to think and plan ahead.
- Computer literate must be familiar with current software such as Microsoft Office, Excel.
- Strong interpersonal and communication skills, listening skills, problem solving skills and conflict resolution skills.
- Lean Certification is a plus.
- Working knowledge of budgets, inventory management and scheduling.
- Background with manufacturing methods such as Kaizen training, process improvement programs and procedures.
- Working knowledge of HACCP and SQF - HACCP & SQF certification preferred
- Working knowledge of food industry and applicable regulations. IBWA CPO certification preferred.