Shift Coach/Shift Lead - Covington
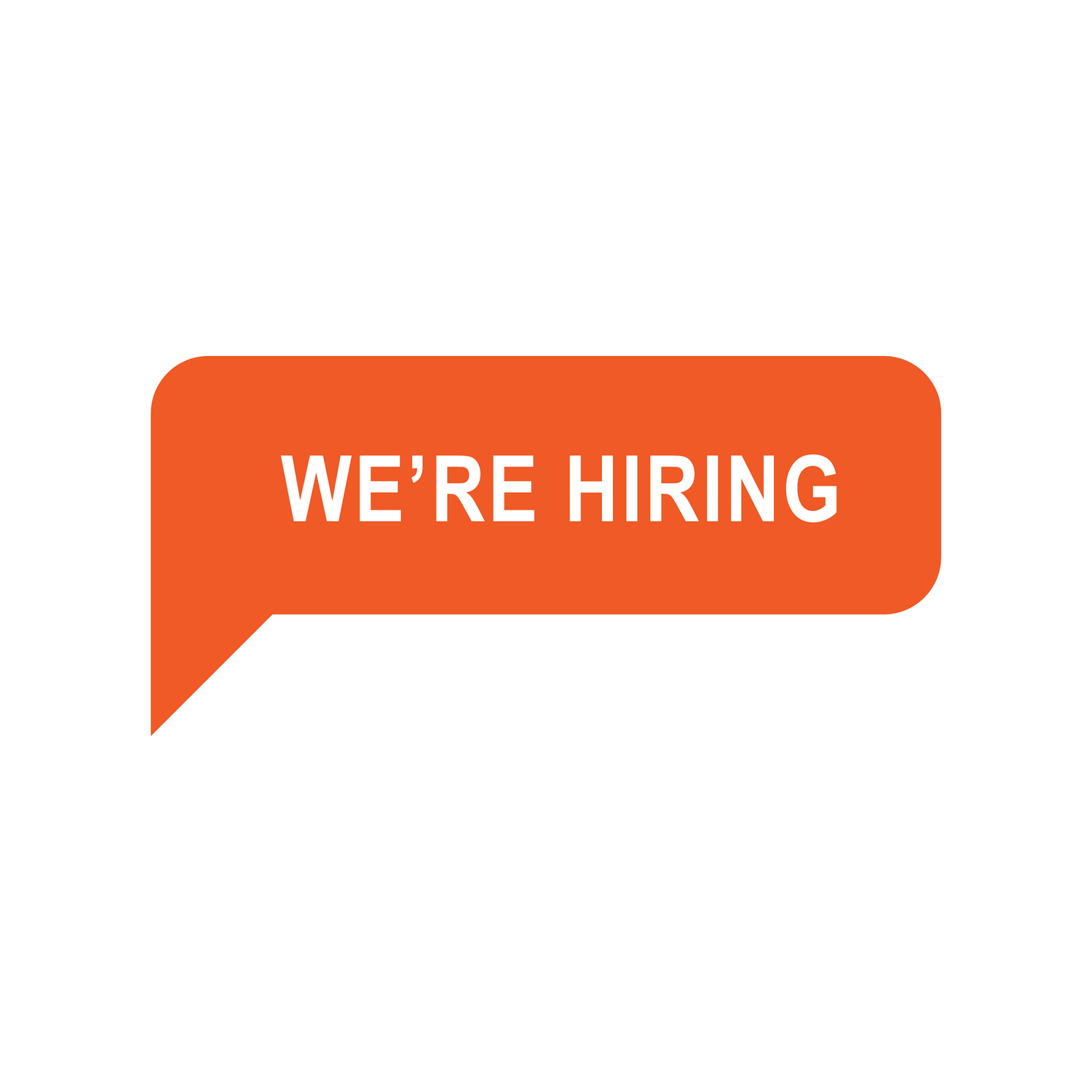
Sugaright
2024-11-15 02:53:22
Covington,
Tennessee,
United States
Job type: fulltime
Job industry: Manufacturing Operations
Job description
Description:
TITLE: Shift Coach/Shift Lead
REPORTS TO: Assistant Plant Manager
LOCATION: Plant Facility
Document Date: 03/10/2014
Job Purpose Summary:
- This position is responsible for all aspects of production during a shift necessary to ensure that orders and production planning goals are met. This role is critical for the coordination of all positions under their area of responsibility for this purpose. This position must be able to operate and if necessary perform all functions in their area of operation if required. This position covers the lab functions, testing and team oversight for analysis when a QA Lab Technician is not present. This position requires the ability to lead and execute the objectives of the company through a team of individuals trained and mentored on their shift. Responsible for the understanding, training and execution of company policies and procedures. If needed, this position is the key role for escalation of issues or corrective actions that Management needs to be aware of and is the representative of the company in certain situations This position is also responsible for the safe and clean operation of activities within their area of responsibility and of their team.
Essential Responsibilities:
- Lead all activities necessary during a shift to manage inventory, traceability, product integrity and compliance to standards.
- Work closely with the Inventory Manager to ensure all orders on a constantly changing schedule are met.
- Follow proper Work Instruction procedures for the management of liquid and specialty liquid sugar, lab testing for conformance to specification and all aspects of product integrity.
- Ensure the integrity of product if source material is an issue.
- Troubleshoot and correct production or mechanical issues on the floor.
- Promote and expect a safe work environment at all times.
- Review and sign off on all load documentation prior to shipping. Work with lab to verify results as required.
- Develop and train staff according to company objectives. Review and mentor staff according to plan.
- Be able to perform all lab chemical testing procedures and troubleshoot issues.
- Ensure the proper security of the facility at all times for biosecurity purposes
- Oversee and assist with the maintenance of equipment as directed and ensure the work area is clean at all times.
- Operate and maintain a forklift or other equipment for positioning or managing material as needed.
- Sample product as required by Quality instructions and perform qualified testing as required.
- Follow GMP and other quality processes and procedures.
- Perform sanitation on equipment as required.
- Perform other duties as assigned
Jobs Supervised (by title):
- Warehouse Receiving Operator
- Bagging Operator
- Jockey/ Truck Washing Operator
- Melting Operator
- Filtration Operator
- Specialty Product Manufacture Operator
- Load-Out Operator
Minimum Qualifications:
A. Education and Experience:
- Ability to work in a food manufacturing environment;
- Previous food industry experience is preferred in excess of five years;
- Supervisory experience in a food manufacturing environment preferred;
- Ability to communicate in English effectively, Multi-lingual preferred (Spanish)
B. Knowledge, Skills and Abilities:
- Must be adaptable and flexible;
- Ability to lead and mentor a cross functional team;
- Ability to communicate and understand expectations for role;
- Ability to work independently;
- Manager the expectations of the company and react to issues;
- Ability to recognize and escalate issues to Management as needed;
- Recordkeeping / documentation skills;
- Basic understanding of laboratory testing equipment;
- Basic understanding of documentation needed for process;
- Basic State, FDA, OSHA and other regulatory understanding as applied to floor operations,
Nonessential Qualifications:
- N/A
Materials and Equipment Directly Used:
- Forklifts and other manufacturing equipment for the receiving, movement and management of materials and granular sugar in totes or bags if needed;
- Office machinery including: Calculator, computer, printers, copiers, etc.
Working Environment / Physical Demands:
The physical demands and work environment characteristics described here are representative of those that must be met by an employee to successfully perform the essential functions of this job. Reasonable accommodations may be made to enable individuals with disabilities to perform the essential functions.
Physical Demands:
Requires prolonged standing, bending, stooping and climbing.
Requires eye-hand coordination and manual dexterity sufficient to operate manufacturing equipment, keyboard, photocopier, telephone, calculator, and other equipment.
Requires normal range of hearing and vision (including colors) to record, prepare and communicate appropriate reports and laboratory results.
Requires lifting up to 75+ pounds. Requires exposure to machines, chemicals and solvents.
Work Environment:
Work environment can be hot, humid, dusty or cold depending on the time of year. Employees may be required to work in or outside of the building depending on the needs of the role.
Due to the nature of liquid sucrose, bees may be present in the work area during certain times of the year.
Must understand vague and implicit instructions and react favorably in all work situations.
Must be mentally adaptable and flexible in dealing with a variety of people and conditions.
Emotional stability and personal maturity are important attributes in this position.
Must understand people and be able to communicate effectively.
Ability to do basic math calculations as required.
PIf6db265a85be-3472