RELIABILITY TEAM LEADER
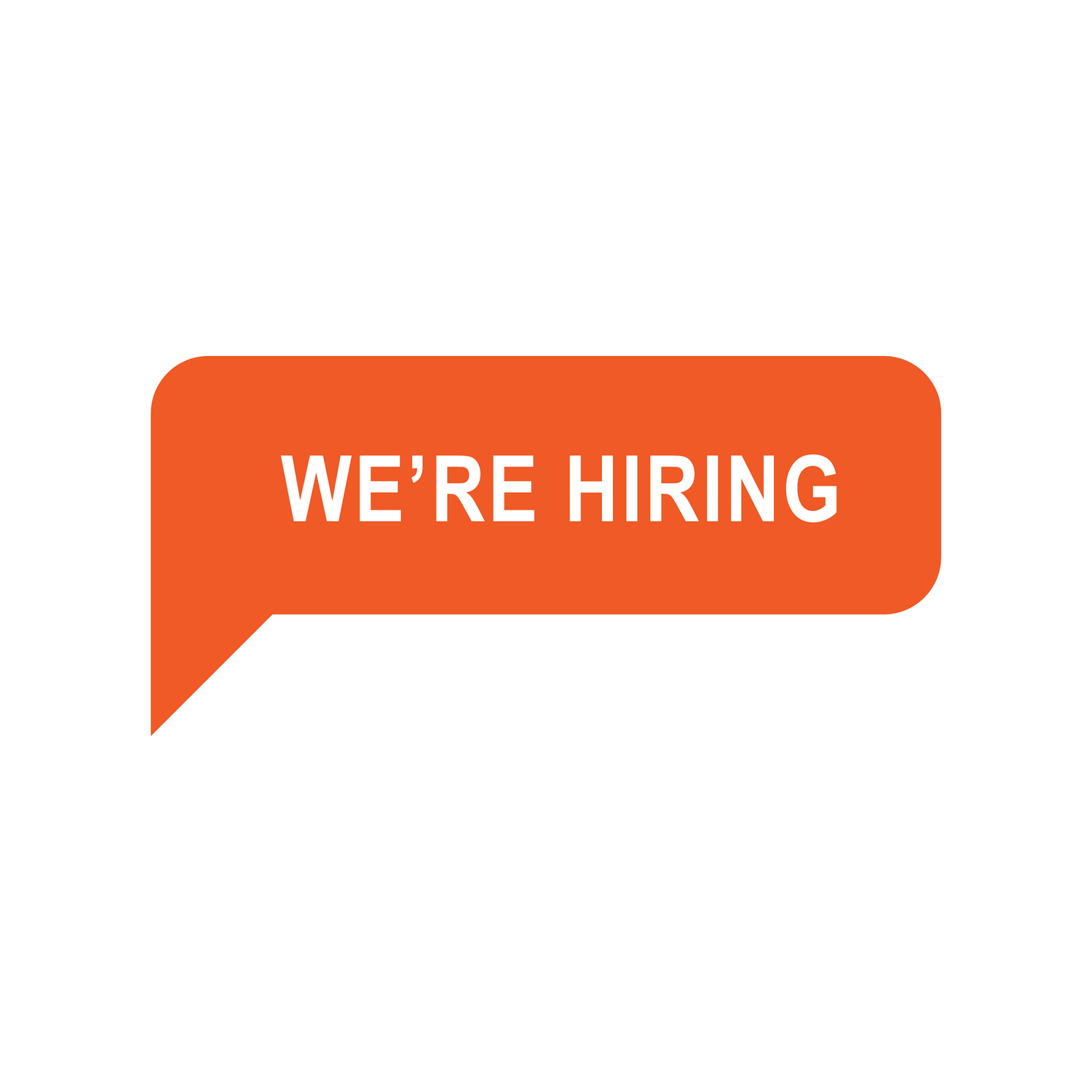
Magnera
2024-11-07 07:43:11
Benson,
North Carolina,
United States
Job type: fulltime
Job industry: Trades & Services
Job description
Responsibilities:
Responsible for uptime of process, ancillary, and facilities equipment. Will ensure all equipment is safe to operate, and will lead continuous improvements efforts for the team. Will serve as a site resource for preventive and predictive maintenance and will lead technical, problem-solving efforts.
Ensure compliance to all safety policies and procedures.
Ensures team members and contractors work safely and comply with all safety policies.
Maintains drawings for site equipment.
Maintains ISO compliant maintenance records for site equipment.
Identifies chronic yield, uptime, and productivity issues and identifies corrective actions to address.
Assists with budget preparation.
Implements preventive and predictive maintenance to improve productivity and reduce costs.
Prepares cost justifications for projects.
Participates in identifying and developing training to ensure department has skills needed to support the business.
Participate in, support and champion safety initiatives.
Support and maintain a culture of continuous improvement, quality, high performance and process excellence
Assist with site regulatory compliance.
Partner with Operations Team, asking for clarification and conferring with the requestor for additional clarification when needed.
Originate and process emergency work orders when needed
Validates & documents all modifications made equipment
Assists in writing and updating standard maintenance procedures.
Familiarizes self with new equipment and assists in training other technicians.
Stays informed of process changes which may affect the normal operation of the equipment.
Assists large installations and equipment modification projects.
Maintains a team effort attitude and approach.
Leads and supports the effective implementation of investment projects approved for capacity or facility expansion and upgrades.
Leads 6s and TPM initiatives.
Understands and implements strategic management aspects of reliability engineering, its relationship to safety and quality, its impact on customer satisfaction, the consequences of failure and the potential for liability.
Plans for reliability programs and integrates various engineering and operational systems to achieve overall program goals and alignment with organizational goals.
Develops models to analyze and predict performance using block diagrams, physics of failure, apportionment, dynamic of reliability, and simulations
Develops reliability test plans that represent the expected use environment and operational conditions.
Identifies, collects, analyzes and manages various types of data to minimize failures and improve performance. Uses failure analysis and other types of root cause analysis in support of reliability.
Provides backup for Maintenance Leader
Trains designated backup and others as identified in all tasks.
Additional duties as assigned.
Supervisory Responsibilities:
This statement considers the intensity and frequency that work is monitored: daily, weekly, monthly, etc.
Supervision Received: Limited supervision
Supervision Given: Backup for Maintenance Team Lead
Qualifications:
Qualifications: "To perform this job successfully, an individual must be able to perform each essential duty satisfactorily. The requirements listed below are representative of the knowledge, skill, and/or ability required. Reasonable accommodations may be made to enable individuals with disabilities to perform the essential functions."
Education: Bachelor of Science in Engineering; Mechanical Engineering, preferred Must have a combination of training and experience which provides the required knowledge, skills and abilities.
Certifications:
Professional certification preferred (TPM, CMRT or other relevant certification)
Six Sigma Black or Green Belt preferred
OSHA 10 Hour Certification
Certified or eligible to become certified CPR/First Aid / BBP
Experience: Minimum of 3 years in Maintenance, Reliability or related field preferred.
Physical/Cognitive Requirements: Work is performed in an office environment and on the plant floor with frequent contact with others. Requires prolonged sitting and frequent bending, stooping and stretching, manual dexterity, the ability to distinguish letters, occasional lifting up to 50 pounds, and the use of office equipment.
Equipment:
Knowledge of and skills in the use of office machines (computer and copier) and business procedures. Manufacturing equipment to include extrusion equipment, winders, instrumemtation & controls, fanuk robotic equipment, hydrolics, pneumatics, and other normal manufacturing tools.
Work Environment:
Job functions will be performed in and around production lines, warehouse, silos', pumping stations, and office areas.
Internal and External Contacts:
This position will interface with the plant workforce and management team. There could also be interaction with outside contractors as needed.
Disclaimer: "The above statements are intended to describe the general nature and level of work to be performed. The above statements are not intended to be construed as an exhaustive list of all responsibilities, duties and skills required of the incumbent in this position. Management retains the discretion to add to or change the duties of the position at any time."