Please scroll down, To apply
Quality Control Manager
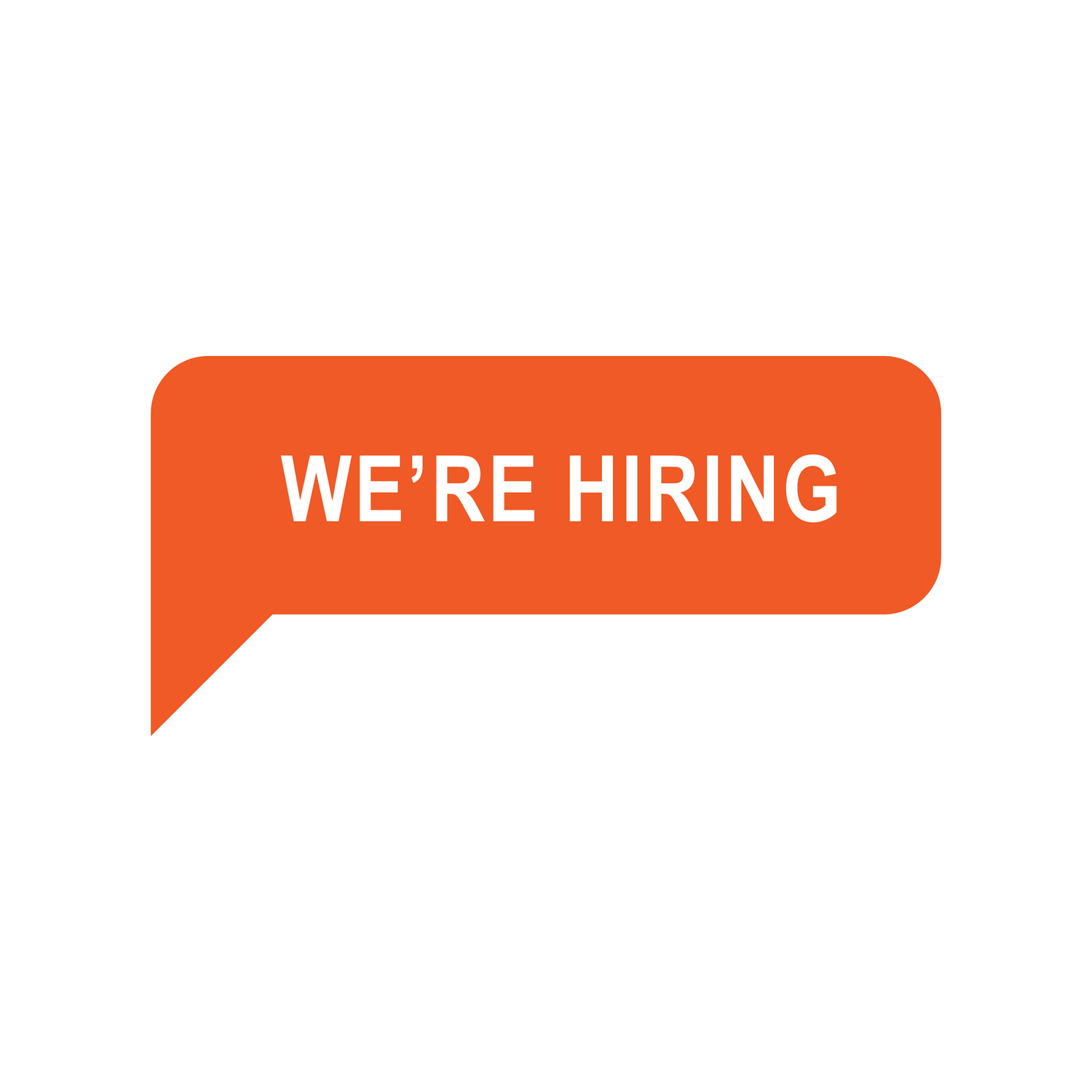
Amber People
2024-09-21 16:40:36
Phoenix,
Arizona,
United States
Job type: all
Job industry: Manufacturing Operations
Job description
Quality Control Manager
location: Phoenix, Arizona
Industry: Medical / Healthcare
The Quality Control Manager (QC) is responsible for the quality control functions and product quality verification for all company facilities.
The Quality Control Manager will supervise and monitor the inspection and testing of materials, parts, and products to ensure adherence to established quality standards. You will also be responsible for establishing inspection protocols, sampling procedures, equipment to be used in the testing process, and suggest improvements, revise quality control policies and procedures, as well as be a knowledge resource for other team members.
Duties and Responsibilities:
- Leads, trains, and coaches Quality Control staff to ensure manufacturing requirements are met
- Act as department communicator during status meetings, management updates, and staff shift changes
- Ensure products are in compliance with professional standards and customer requirements
- Stays up-to-date with CGMPs, FDA, NSF and other regulatory guidelines
- Signs off on verifications, packets, logs, and other documentations
- Approves incoming materials by confirming specifications; laboratory testing, conducting visual, organoleptic and measurement tests; rejecting and returning unacceptable materials
- Responsible for creating C of A s for internal test results as well as releasing C of A s from 3rd party laboratories
- Writing and finalizing Master Manufacturing Record (MMR s)
- Collaborating with R&D personnel to document and finalize future products and processes
- Responsible for administering the company quality control program in accordance with customer and company requirements
- Determine, establish and enforce, through all operational departments, quality and safety requirements in accordance with company needs, based on FDA regulations, cGMP, NOP (National Organic Program), and other regulatory guidelines
- Act as liaison with external parties on matters relating to the quality system and support all operational departments
- Participate in organizational committees, such as Osha Safety, Hazard control, Formula change
- Recommends changes in specifications of materials, parts, and products based on inspection results
- Help develop in-house training material related to regulatory statutes
- Responsible for the training of personnel in cGMPs and overseeing audits
- Oversees audits and/or quality regulatory inspections
- Assure that all documentation is maintained, updated, reviewed and approved to reflect current processes
- Assure that all consumer complaints are recorded properly and are closed out upon resolution
- Assure all components and raw materials meet specifications for use in processing of intermediate and final product by documented methods of sampling, testing, formulation, labelling, storage, distribution, and approvals
- Assure that all process errors, product failures and any process deviations are investigated and that any corrective actions and/or preventive actions are carried out
- Responsible for creating CAPA s and participating in root cause investigation
- Help develop laboratory necessities and/or research laboratory equipment
<!– job description page –>